MOTEK Screening Bucket in Iron Ore Screening
Release time: 2025-03-28
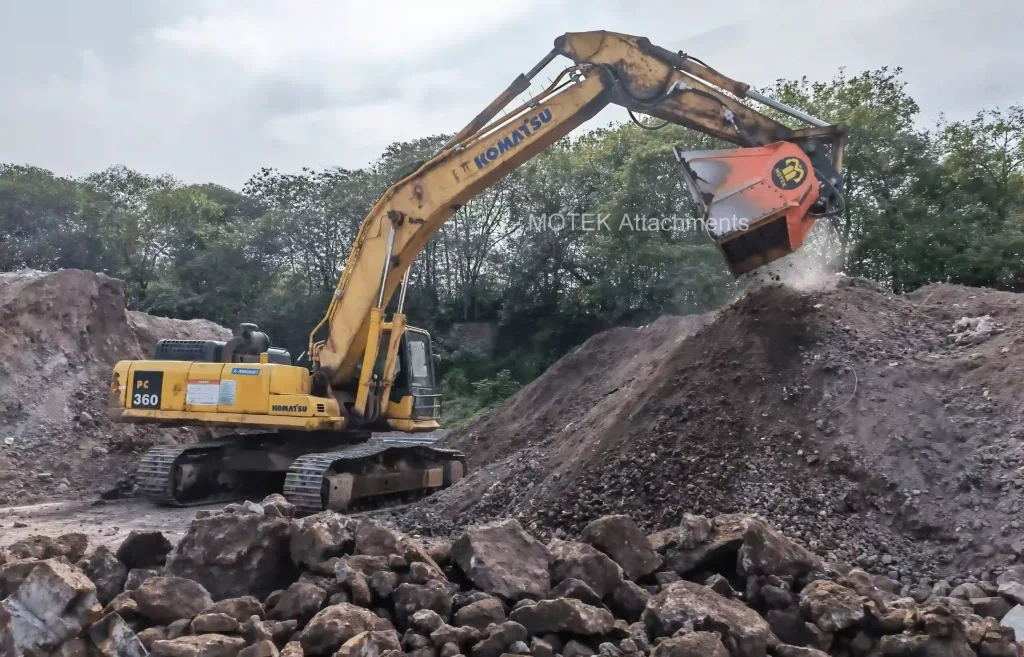
In the field of iron ore mining and processing, screening and crushing are the core links that determine production efficiency and economic benefits. Traditional processes usually use a combination of fixed crushing stations and screening equipment, which has complex processes, high energy consumption and insufficient flexibility. MOTEK screening and crushing bucket, as a mobile equipment that integrates crushing and screening functions, is gradually becoming an innovative solution in the field of iron ore screening with its high efficiency, flexibility and environmental protection.
Efficiency improvement: shorten production cycle and release production capacity potential
1. Integrated process reduces intermediate links: Traditional iron ore screening requires a multi-stage process of “mining → transportation → coarse crushing → screening → secondary crushing → re-screening”, while the screening crushing bucket can directly complete crushing and screening synchronous operations at the mining site. For example, after an Australian iron ore mine adopted a screening crushing bucket, the processing capacity of a single device reached 150-200 tons per hour, the screening efficiency increased by 30%, and the production cycle was shortened by more than 40%.
2. Accurate classification improves ore utilization: MOTEK screening crushing bucket realizes instant classification of iron ore through an adjustable screen (usually 10-100mm aperture). Taking magnetite as an example, the equipment can quickly separate high-grade lump ore (directly used for smelting) and low-grade crushed ore (entering the re-grinding process), reducing ineffective crushing energy consumption, and increasing the comprehensive utilization rate of ore to more than 95%.
3. Mobility adapts to dynamic mining scenarios: In open-pit mines, the distribution of ore veins often changes with the progress of mining. MOTEK screening buckets for excavators can be directly loaded on the excavator or loader and move with the mining face, avoiding repeated adjustment of the position of fixed equipment, and extending the effective working time per day by 2-3 hours.
Cost Optimization: Cost Reduction and Efficiency Improvement throughout the Life Cycle
1. Reduce Transportation and Storage Costs: The traditional process requires the raw ore to be transported to a fixed crushing station, while MOTEK screening buckets can produce finished ore of qualified particle size on site. Taking an iron mine in Anshan, China as an example, after adopting MOTEK screening crushing bucket, the transportation volume was reduced by 50%, and the annual fuel and vehicle maintenance costs were saved by more than 1.2 million yuan.
2. Reduce Equipment Investment and Maintenance Costs: MOTEK screening bucket for loader can replace multiple equipment such as jaw crushers, cone crushers, and vibrating screens in traditional processes. According to calculations by Vale of Brazil, the equipment procurement cost is reduced by 35%, the maintenance manpower demand is reduced by 60%, and there is no complex conveyor belt system, and the failure rate is reduced by 70%.
3. Extend the service life of equipment: MOTEK padding bucket adopts high manganese steel wear-resistant lining and hydraulic overload protection technology. Under the conditions of high hardness and high abrasiveness of iron ore, the life of core components can reach 8000-10000 hours, which is more than twice that of traditional equipment.
Environmental Benefits: Assisting Green Mine Construction
1. Reduce Dust and Noise Pollution: The closed screening structure is combined with a spray dust suppression system to reduce the dust concentration at the work site to less than 10mg/m³ (the national standard requirement is ≤20mg/m³); the hydraulic drive mode reduces noise by 15-20 decibels compared to traditional diesel-powered equipment, meeting the environmental protection requirements of mining areas around residential areas.
2. Reduce Carbon Emissions and Energy Consumption: MOTEK screening and crushing bucket driven by electricity or hybrid power reduces the energy consumption per ton of ore by 40% compared to diesel-powered equipment. If this technology is popularized in the global iron ore industry, annual carbon emissions are expected to be reduced by 12 million tons, which is equivalent to the carbon fixation effect of planting 600 million trees.
3. Reduce Land Occupancy and Ecological Damage: There is no need to build fixed crushing stations and stockpiles, which can reduce the hardened ground area of the mining area by 30%-50%, reduce damage to surrounding vegetation and water systems, and help mine ecological restoration.
Adaptability expansion: multiple values for dealing with complex working conditions
1. Handling high-viscosity and high-water content ores: Traditional vibrating screens are easily blocked by wet ore materials, while MOTEK screening and crushing bucket uses a rotating screen drum + high-frequency vibration technology, which has been successfully applied to the screening of high-humidity hematite in the rainy season in West Africa. The screening efficiency of ore with a moisture content of 15% remains above 85%.
2. Adapt to small-scale and dispersed ore bodies: For small and medium-sized iron ore or tailings redevelopment projects, the modular design of MOTEK screening and crushing bucket supports rapid deployment, and the investment recovery period can be shortened to 8-12 months. A 300,000 tons/year iron ore mine in Peru achieved a profit cycle 6 months earlier through this equipment.
Technological iteration drives the upgrading of the iron ore industry
The application of MOTEK excavator screening bucket not only solves the efficiency bottleneck of iron ore screening, but also reconstructs the logic of mine production through the technical route of “mobility, integration, and intelligence”. As the global mining industry transforms towards greening and refinement, this equipment will become one of the core tools to enhance the competitiveness of iron ore companies. In the future, combined with innovative technologies such as 5G remote control and hydrogen energy power, screening and crushing buckets are expected to further promote iron ore mining into a new era of “zero carbon and high efficiency”.