Advantages and Economic Value of Crusher Bucket in Narrow Space Operation
Release time: 2025-03-25
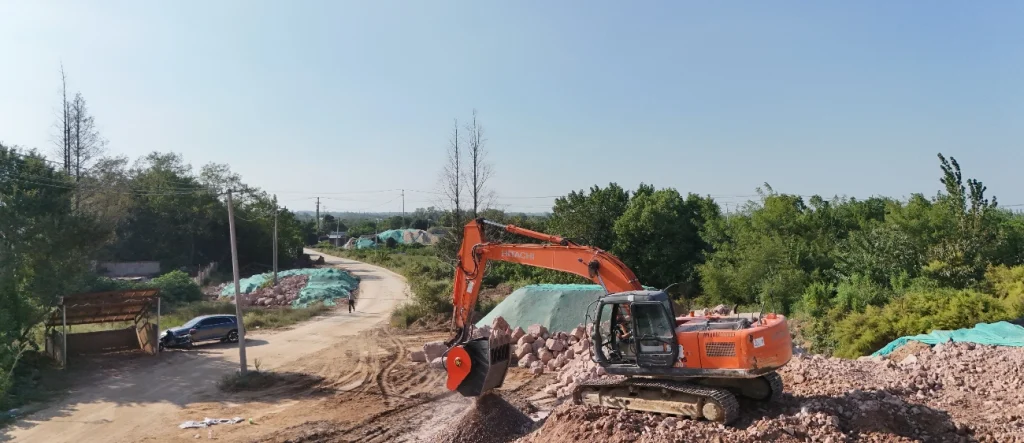
Against the background of accelerated urbanization and intensive development of underground space, the disadvantage of traditional crushing equipment being limited by the operating radius has become increasingly prominent. As a modular crushing device, MOTEK crusher bucket has become an important technical solution for narrow space construction such as underground tunnels, building foundation pits, and mine tunnels with its unique structural design and operation mode. This article systematically analyzes its core advantages in restricted environments from the dimensions of technical performance, economic benefits, and safety control.
Spatial adaptability to reconstruct the operation scene
Minimalist motion radius achieves zero dead angle operation: MOTEK crusher bucket adopts a hydraulic drive system directly connected to the main engine, and the overall operation unit length can be controlled within the range of 2.5-4 meters (depending on the main engine model). Compared with the 12-15 meter operation deployment length of the traditional mobile crushing station, its turning radius is reduced by more than 60%, and the material crushing and loading combined operation can be completed in a 2.5-meter wide tunnel. A typical example is a subway tunnel renovation project in Shenzhen, where MOTEK crushing bucket completed the demolition of the concrete structure in a tunnel with a net height of 3.2 meters, avoiding the vibration damage of the existing structure caused by traditional blasting technology.
Modular design breaks through site limitations: Through the quick-change system, MOTEK crushing bucket can complete the adaptation conversion with the excavator and loader within 20 minutes. This “one machine for multiple uses” feature enables it to switch between crushing, screening, and loading functions in a narrow space, reducing the number of equipment entering the site. Statistics show that the configuration of underground engineering equipment using crushing buckets is reduced by an average of 40%, and the site area occupied is reduced by 65%.
Process innovation improves work efficiency
In-situ crushing technology reduces transportation costs: MOTEK crushing bucket supports the integrated “crushing-backfilling” operation mode, which can crush the demolished concrete, rock and other materials into 0-50mm graded aggregates on site and directly use them for foundation cushion construction. Taking an underground parking lot expansion project as an example, the application of this technology has reduced the amount of construction waste transported by 82%, the material recycling rate has reached 95%, and the comprehensive cost has been saved by 370,000 yuan/thousand cubic meters.
Precise crushing control ensures construction quality: The hydraulic breaker equipped with a pressure compensation system can achieve precise pressure adjustment of 0.5-1.2MPa, and with a 360° rotating mechanism, the crushing error can be controlled within the range of ±5cm. This fine operation capability shows unique value in the renovation of cultural relics protection buildings and pipeline-intensive areas.
Safety performance creates management value
Intrinsically safe design reduces accident risks: MOTEK crushing bucket adopts a closed crushing chamber structure, and with an automatic overload protection device, the amount of splashing can be reduced by more than 90%. Compared with the traditional crushing process, the dust concentration on the working surface is reduced from 28mg/m³ to 6mg/m³, and the noise level is controlled from 112dB(A) to less than 85dB(A), which significantly improves the working environment in confined spaces.
Full-cycle cost advantage analysis
Optimization of equipment input-output ratio: Taking a 20-ton excavator equipped with a crushing bucket as an example, the initial investment is about 450,000 yuan, and the average daily processing volume can reach 300-500 cubic meters. Compared with the mobile crushing station (investment of about 1.5 million yuan) + transportation vehicle combination required by traditional processes, the investment recovery period is shortened from 18 months to 10 months, and the annual comprehensive rate of return is increased to 28%.
Structural reduction in operation and maintenance costs: MOTEK crushing bucket attachment adopts a wear-resistant alloy cutter disc design. When crushing C30 concrete, the tool life can reach 8000-12000m³, and the replacement cost is 40% lower than that of traditional hammers. Its modular structure controls the replacement time of major components within 2 working hours, and the maintenance efficiency is increased by 70% compared with the integral crusher.
Environmental friendliness expands the application boundary
Low-carbon process is in line with sustainable development: In-situ crushing technology reduces carbon emissions generated by material transportation, and CO₂ emissions can be reduced by about 58 tons per 10,000 tons of construction waste treatment. Under the EU CE certification system, the energy consumption index (ECI) of modern crushing buckets has dropped to 0.32kWh/t, reaching the industry-leading level.
Vibration control protects surrounding structures: Through the combination of hydraulic buffer system and frequency tuning technology, the vibration transmission attenuation rate of crushing bucket operation is increased by 65% compared with impact crushing. In a deep foundation pit project in Shenzhen close to an operating subway line, monitoring data showed that the construction vibration speed was always controlled below 2.5mm/s, which is lower than the 5mm/s limit required by the subway tunnel protection standard.
The excellent performance of MOTEK hydraulic crushing bucket in narrow space is essentially the dialectical unity of “space compression” and “function expansion” achieved through technological innovation. The equipment is evolving from a simple crushing tool to an intelligent construction solution for space-constrained scenarios. For urban builders, having this intensive construction equipment means obtaining the key technical key to solving the space dilemma in the context of increasingly scarce land resources.